“un tempo si costruiva per l’eternità, adesso ci si accontenta di 50 anni.”

Sarà capitato a tutti passando davanti ad un cantiere di notare come i ferri di armatura siano già arrugginiti prima ancora di essere posizionati e gettati. E sicuramente i più hanno pensato “non va bene!”. Ammetto di esserci caduto anche io le prime volte ma in realtà la patina sottile che ricopre le armatura è una pellicola che le protegge. Dopo il getto, grazie al PH del cemento nelle prime fasi di vita (all’incirca di 12,5-12), si ha un fenomeno rilucente del ferro che ne migliora le caratteristiche e in pratica lo rende passivato. Con il passare degli anni l’anidride carbonica reagisce con l’idrossido di calcio presente nella malta generando carbonato di calcio ed acqua:
CO2+Ca(OH)2 → CaCO3+H20
-
Abbassamento del PH (8,5), quindi esposizione delle armature alla corrosione;
-
Contrazione della pasta, quindi fessurazione,
-
Aumento della resistenza e della durezza del cemento.
Quindi la carbonatazione non ha un effetto direttamente negativo sul cemento (ne aumenta le prestazioni) ma favorisce la corrosione dell’acciaio.
La corrosione dell’acciaio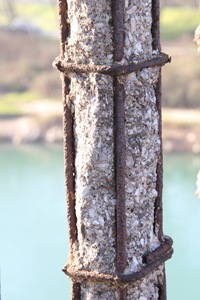
Quando l’acciaio si ossida aumenta di 5 volte il proprio volume. Questo aumento di volume crea fortissime pressioni laterali che tendono a lesionare il cemento e, con un processo degenerativo, ad espellere il copriferro esponendo sempre di più le armature agli attacchi ambientali che arrugginiranno rapidamente andando a diminuire la loro sezione resistente.
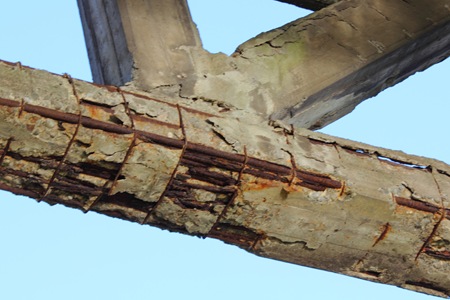
Questo è il grosso inconveniente dell’acciaio.
Nelle opere di consolidamento, specie per beni di valore storico, si utilizza acciaio inox (che ha un costo superiore di 4 volte circa dell’acciaio ordinario.
Anche l’acciaio inox arrugginisce, però ha un aumento di volume molto ridotto.
Determinare lo spessore dello strato carbonatato
E’ possibile determinare la profondità di carbonatazione con esame visivo dell’elemento, con test colorimetrico con soluzione all’1% di fenolftaleina in alcool etilico. Le carote devono essere spaccate secondo piani normali alla superficie di esposizione e, dopo essere state pulite dalle polveri, vanno spruzzate con una soluzione di fenolftaleina all’1% in alcool etilico. La fenolftaleina vira al rosso al contatto con materiale a pH > 9,2 (calcestruzzo sano) e rimane incolore per valori di pH inferiori
Valutare la vita utile di una struttura in cemento armato
La carbonatazione penetra nel calcestruzzo seguendo questa legge:

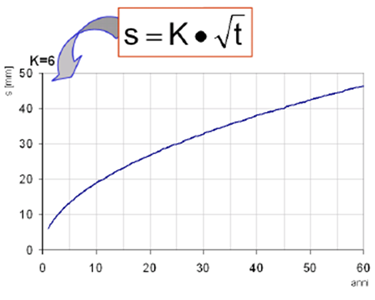
- t= tempo espresso in anni
- s= spessore carbonatato in millimetri
- K= coefficiente di velocità di penetrazione [mm/anno(1/n)]
- n= coefficiente in funzione della porosità (per calcestruzzi mediamente porosi n=2)
- Si misura la profondità del fronte carbonato s al tempo t;
- Si ricava il coefficiente di velocità di penetrazione;
- Si costruisce la curva s=s(t) da cui individuiamo la vita residua.
La durabilità del cemento armato
La durabilità dipende dalla permeabilità all’acqua che è legata al tipo di inerti, alla classe del cemento ed al rapporto acqua-cemento del conglomerato.
Per capire l'importanza del rapporto acqua cemento è interessante osservare la tabella sottostante che mostra per i vari rapporti acqua/cemento (ordinate) e copriferro (ascisse espesso in mm) il tempo, espresso in anni, che impiega la carbonatazione per raggiungere i ferri di armature.
A/C - c
|
5
|
10
|
15
|
20
|
25
|
30
|
0,45
|
19
|
75
|
+100
|
+100
|
+100
|
+100
|
0,50
|
6
|
25
|
56
|
99
|
+100
|
+100
|
0,55
|
3
|
12
|
27
|
49
|
76
|
+100
|
0,60
|
1,8
|
7
|
16
|
29
|
45
|
65
|
0,65
|
1,5
|
6
|
13
|
23
|
36
|
52
|
0,70
|
1,2
|
3
|
11
|
19
|
30
|
43
|
Poiché la porosità del calcestruzzo è direttamente proporzionale all’acqua di impasto, basse prestazioni meccaniche sono generalmente sinonimo di scarsa durabilità.
Ripristino di elementi in c.a. carbonatati
Dopo aver visto il fenomeno della carbonatazione delle strutture in cemento armato in questo articolo vedremo come intervenire per consolidare gli elementi ammalorati.
Le fasi dell’intervento
- Demolizione delle parti decoese o poco resistenti tramite idrodemolizione o attrezzi manuali fino al raggiungimento dello spessore del copriferro;
- Valutazione della profondità di carbonatazione (vedi articolo) e demolizione fino al raggiungimento della zona non carbonatata;
- Scarnificazione meccanica della superficie sana per lo spessore di 1cm. per la realizzazione di un sottofondo aggrappante;
- Pulitura delle armature dalla ruggine ed eventuale reintegro delle stesse;
- Trattamento dei ferri con due mani di malta cementizia pennellabile bicomponente a base di leganti idraulici; polveri silicee, inibitori di corrosione e dispersione di polimeri acrilici;
- Applicazione di un primer di resina epossidica sulla superficie del calcestruzzo;
- Riporto di malta cementizia a ritiro controllato eventualmente contenente microfibre in polipropilene, da applicarsi con cazzuola o spatola bagnando a rifiuto il sottofondo;
- Regolazione delle delle superfici con malta ad inerti di fine granulometria e additivi amalgamanti con polimeri acrilici in emulsione;
- Verniciatura protettiva.
![]() |
Particolare dell'intervento |
Fonte: Ingegneriaedintorni.com
A cura di Braian.
Riferimenti:
- Appunti del corso di Diagnostica e Consolidamento – Prof. Ing. Anna De Falco
- Concrete Repairs, vol.I.A, Concrete pubblication 1986 (tabella profondità di carbonatazione)